Zinc&Aluminum Die Casting Manufacturer China: Custom High Quality Precision Parts
Zinc and aluminum die casting is a manufacturing process that involves the production of high-quality precision parts. These parts are used in a wide range of industries, including automotive, aerospace, and electronics. China is one of the leading countries in the world when it comes to producing these parts, and there are many manufacturers in the country that specialize in zinc and aluminum die casting.
One such manufacturer is China Custom High Quality Precision Parts. This company has been in business for many years and has a reputation for producing high-quality parts that meet the needs of its customers. The company uses the latest technology and equipment to ensure that its parts are of the highest quality, and it employs a team of skilled professionals who are dedicated to providing excellent customer service.
Whether you need parts for your automotive business or for your aerospace company, China Custom High Quality Precision Parts can provide you with the solutions you need. With its commitment to quality, reliability, and customer satisfaction, this company is a top choice for anyone looking for a reliable and trustworthy zinc and aluminum die casting manufacturer in China.
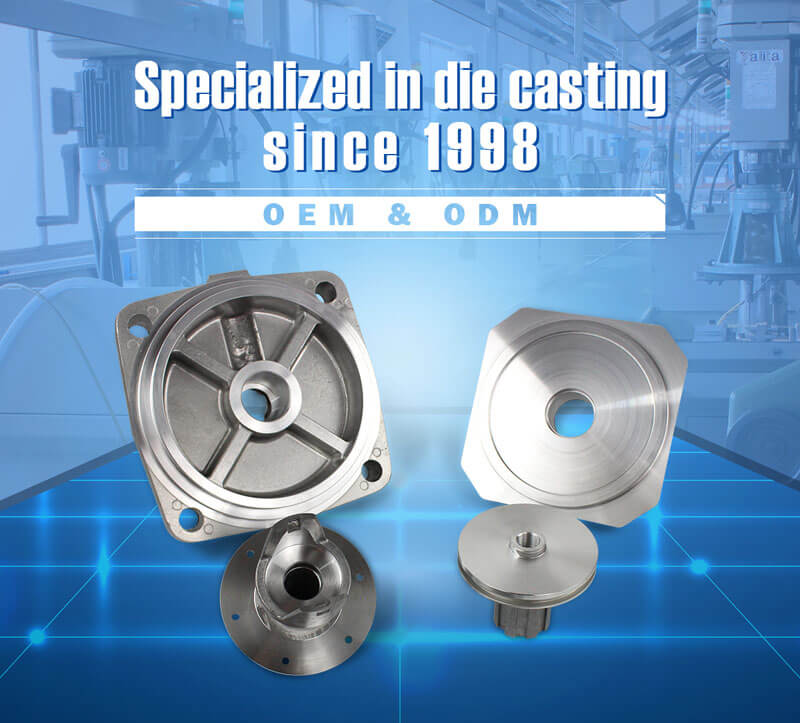
Understanding Zinc & Aluminum Die Casting
Zinc and aluminum die casting are two popular manufacturing processes used to create high-quality precision parts. These processes involve melting metal alloys and injecting them into molds to create specific shapes and designs.
Zinc Die Casting
Zinc die casting is a process that involves melting zinc alloy and injecting it into a mold under high pressure. The mold is designed to create the desired shape and design of the final product. Zinc die casting is a popular choice for creating small to medium-sized parts that require high precision and accuracy.
Zinc is an excellent choice for die casting because of its unique properties. It is a lightweight metal that is easy to work with and has excellent thermal and electrical conductivity. Zinc is also highly resistant to corrosion, making it an ideal choice for parts that will be exposed to harsh environments.
Aluminum Die Casting
Aluminum die casting is a similar process to zinc die casting, but it uses aluminum alloy instead of zinc alloy. Aluminum is a popular choice for die casting because of its strength and durability. It is also lightweight and has excellent thermal and electrical conductivity.
Aluminum die casting is used to create a wide range of products, from small parts to large components. It is an ideal choice for products that require high strength and durability, such as automotive parts, electronic components, and aerospace components.
Advantages of Zinc & Aluminum Die Casting
Zinc and aluminum die casting offer many advantages over other manufacturing processes. Some of the key advantages include:
- High precision and accuracy
- Fast production times
- Low labor costs
- Excellent surface finish
- Wide range of shapes and designs
- High strength and durability
- Lightweight and easy to work with
Overall, zinc and aluminum die casting are excellent choices for creating high-quality precision parts. They offer many advantages over other manufacturing processes and are widely used in a variety of industries.
The Manufacturing Process
Designing
Before the manufacturing process begins, the design of the product is finalized. The Zinc&Aluminum Die Casting Manufacturer China Custom High Quality Precision Parts team works with the client to ensure that the design meets their specifications and requirements. Once the design is confirmed, the team creates a mold for the product.
Molding
The mold is created using a high-quality steel alloy. The mold is then heated to a specific temperature and injected with molten metal. The metal is then allowed to cool and solidify, taking on the shape of the mold. Once the metal has cooled, the mold is opened and the product is removed.
Casting
After the product is removed from the mold, it is inspected for any defects. Any defects are corrected before the product moves on to the trimming stage. The casting process ensures that the product is of high quality and meets the client’s requirements.
Trimming
The trimming stage involves removing any excess material from the product. This is done using a variety of tools, including saws and grinders. The product is then inspected again to ensure that it meets the client’s specifications. Once the product has been approved, it is ready for shipping.
Overall, the Zinc&Aluminum Die Casting Manufacturer China Custom High Quality Precision Parts team is committed to providing high-quality products that meet the client’s requirements. The manufacturing process is designed to ensure that the products are of the highest quality and are delivered on time.
Custom High Quality Precision Parts
When it comes to die casting, custom high-quality precision parts are essential for ensuring the success of any project. These parts are designed to meet specific requirements and are manufactured to precise tolerances, ensuring that they fit perfectly into the final product. In this section, we’ll take a closer look at the various considerations that go into producing custom high-quality precision parts.
Material Selection
The material used for custom high-quality precision parts will depend on the specific requirements of the project. Zinc and aluminum are two of the most commonly used materials for die casting. Zinc is known for its excellent strength and durability, making it ideal for parts that need to withstand a lot of wear and tear. Aluminum, on the other hand, is lightweight and offers good thermal conductivity, making it ideal for parts that need to dissipate heat quickly.
Other factors to consider when selecting a material include cost, corrosion resistance, and machinability. For example, if the part needs to be machined after casting, a material with good machinability will be essential.
Design Considerations
Design is a critical factor when it comes to custom high-quality precision parts. The part must be designed to meet the specific requirements of the project, taking into account factors such as size, shape, and function. The design should also consider any potential manufacturing issues, such as the need for undercuts or the formation of air pockets.
Other design considerations include the type of finish required, any surface texturing or engraving, and the overall aesthetic of the part. These factors will all impact the final appearance and functionality of the part.
Quality Control
Quality control is essential for ensuring that custom high-quality precision parts meet the required standards. This involves a range of testing and inspection procedures, including dimensional checks, surface finish analysis, and material testing. Any defects or issues must be identified and addressed before the parts are approved for use.
In addition to testing and inspection, quality control also involves ongoing monitoring of the manufacturing process. This helps to identify any potential issues early on and allows for adjustments to be made to ensure that the final parts meet the required specifications.
Overall, custom high-quality precision parts are an essential component of any successful die casting project. By carefully considering material selection, design, and quality control, manufacturers can produce parts that meet the specific requirements of their clients, ensuring that the final product is of the highest quality.
Why Choose China for Die Casting Manufacturing
China has become one of the leading countries in die casting manufacturing, and for good reason. The country has a strong manufacturing infrastructure, a skilled workforce, and a competitive cost structure. These factors make China an ideal destination for businesses looking for high-quality die casting services.
One of the key advantages of working with a die casting manufacturer in China is the cost savings. Due to the lower labor costs and economies of scale, Chinese manufacturers are able to offer competitive pricing without compromising on quality. This is especially beneficial for businesses that require large quantities of parts.
Another advantage of working with a Chinese die casting manufacturer is the access to advanced technology and equipment. Chinese manufacturers invest heavily in research and development to stay ahead of the competition and provide their customers with the latest advancements in die casting technology. This ensures that the parts produced are of the highest quality and meet the customer’s specifications.
In addition, Chinese manufacturers have a reputation for producing high-quality parts with tight tolerances. They have strict quality control processes in place to ensure that each part meets the required specifications. This is important for businesses that require precision parts for their products.
Overall, choosing a Chinese die casting manufacturer for high-quality precision parts can provide businesses with a competitive advantage. With lower costs, access to advanced technology, and a reputation for high-quality parts, it’s no wonder that more and more businesses are turning to China for their die casting needs.
Selecting the Right Manufacturer
When it comes to selecting a Zinc&Aluminum Die Casting Manufacturer in China, there are several factors to consider. Choosing the right manufacturer is crucial to ensure that you receive high-quality precision parts that meet your specifications. Here are some key considerations to keep in mind:
Experience
One of the most important factors to consider when selecting a manufacturer is their experience in the industry. Look for a manufacturer that has a proven track record of success and a long history of producing high-quality parts. A manufacturer with years of experience will have the expertise and knowledge needed to handle complex projects and ensure that your parts are produced to your exact specifications.
Quality Assurance
Quality assurance is another critical factor to consider when selecting a manufacturer. Look for a manufacturer that has strict quality control processes in place to ensure that every part meets your specifications. Ask about their quality control procedures and certifications, such as ISO 9001, to ensure that they meet industry standards.
Pricing
Pricing is always a consideration when selecting a manufacturer, but it should not be the only factor. Look for a manufacturer that offers competitive pricing while still maintaining high-quality standards. Be wary of manufacturers that offer significantly lower prices than their competitors, as this may indicate lower quality or subpar materials.
In summary, selecting the right Zinc&Aluminum Die Casting Manufacturer in China requires careful consideration of several factors, including experience, quality assurance, and pricing. By taking the time to research and evaluate potential manufacturers, you can ensure that you receive high-quality precision parts that meet your specifications.
Conclusion
In conclusion, Zinc&Aluminum Die Casting Manufacturer China Custom High Quality Precision Parts is a reliable and efficient option for businesses in need of custom die-cast parts. With a focus on precision and quality, these manufacturers offer a wide range of services to meet the needs of various industries.
The use of zinc and aluminum alloys in die-casting offers several advantages, including high strength, durability, and corrosion resistance. Additionally, the precision and accuracy of the die-casting process ensure that each part meets exact specifications, reducing the need for additional machining or finishing.
When choosing a die-casting manufacturer, it is important to consider factors such as experience, expertise, and quality assurance processes. By working with a reputable manufacturer, businesses can ensure that their parts are produced to the highest standards and delivered on time.
Overall, Zinc&Aluminum Die Casting Manufacturer China Custom High Quality Precision Parts is a valuable resource for businesses seeking reliable and high-quality die-cast parts. With a commitment to precision, quality, and customer satisfaction, these manufacturers offer a range of services to meet the needs of various industries.